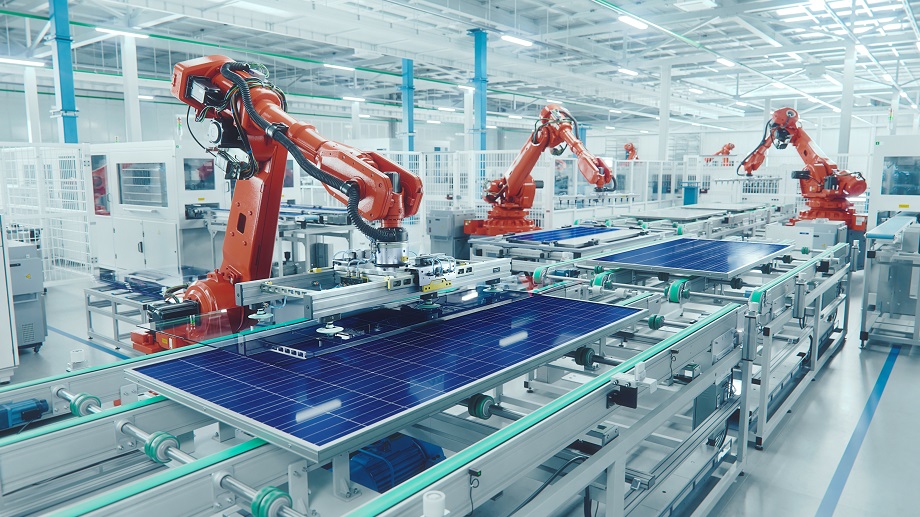
Manufacturing automation is transforming the way products are made, influencing nearly every aspect of production and supply chains worldwide. It’s not just about replacing human labor with machines; automation entails integrating advanced technologies, smart systems, and robotics to optimize efficiency, improve quality, reduce waste, and enable greater scalability in manufacturing processes. As the fourth industrial revolution—often referred to as Industry 4.0—continues to evolve, manufacturing automation is at the forefront of this change.
Defining Manufacturing Automation
Manufacturing automation refers to the use of various control systems, such as computers or robots, and information technologies to handle different processes and machinery in an industry. It aims to streamline operations, reduce manual intervention, and boost productivity while maintaining high levels of precision. The ultimate goal is to make production processes more efficient, cost-effective, and reliable, while simultaneously freeing up human workers to focus on tasks requiring creativity, problem-solving, and innovation.
Automation in manufacturing can vary in complexity, ranging from simple robotic arms performing repetitive tasks, to sophisticated fully automated factories that operate with minimal human involvement. It is driven by several technologies, including artificial intelligence (AI), robotics, machine learning (ML), the Internet of Things (IoT), and big data analytics. These technologies enable automated systems to not only perform tasks but also to monitor, analyze, and optimize their own performance.
Historical Context and Evolution of Automation
Automation in manufacturing has its roots in the Industrial Revolution, when mechanical systems began to replace manual labor. The invention of machines like the steam engine and spinning jenny paved the way for mass production. In the 20th century, the introduction of the assembly line by Henry Ford in 1913 marked another significant leap toward automation by dividing tasks into simple, repeatable steps that machines or workers could perform quickly and efficiently.
However, it wasn’t until the advent of computers and programmable logic controllers (PLCs) in the mid-20th century that automation truly began to transform manufacturing. The development of robotics in the 1960s and 1970s brought about further advancements, enabling machines to handle more complex and dangerous tasks that were previously beyond the scope of human capability.
Today, with the rise of Industry 4.0, automation is becoming smarter, more connected, and increasingly autonomous. Manufacturers are leveraging AI, advanced sensors, and machine learning algorithms to predict failures, optimize processes, and make real-time decisions without human input.
Types of Manufacturing Automation
- Fixed Automation (Hard Automation)
Fixed automation involves using machines or robotic systems that are programmed to perform a specific set of tasks repeatedly, such as on an assembly line. These systems are typically designed for high-volume production and operate at a high efficiency but lack flexibility. Once set up, they cannot easily adapt to changes in production or product design without significant reprogramming or reconfiguration. Fixed automation is common in industries like automotive manufacturing, where identical products are produced in large quantities. - Programmable Automation
This type of automation allows for some flexibility in production. Machines and systems can be reprogrammed to handle different tasks or produce different products, making it ideal for industries that manufacture a variety of goods in small to medium batches. Programmable automation is often used in industries such as electronics or aerospace manufacturing, where customization and variability in production are more common. - Flexible Automation
Flexible automation represents a more advanced level, enabling manufacturers to switch between different products or tasks with minimal downtime and human intervention. These systems can adapt to changes in production schedules or designs without requiring extensive reconfiguration. This is often seen in industries where product lifecycles are shorter, and responsiveness to market changes is critical, such as consumer electronics or pharmaceuticals. - Cognitive Automation
Cognitive automation is the latest evolution in the field, combining AI, machine learning, and IoT to create self-learning, self-optimizing systems. These systems can analyze vast amounts of data, learn from past performance, and make intelligent decisions to improve efficiency, reduce waste, and prevent downtime. Cognitive automation is pushing the boundaries of what automated manufacturing systems can achieve by enabling them to “think” and “adapt” in real-time.
Key Benefits of Manufacturing Automation
- Increased Efficiency and Productivity
Automation drastically increases the speed of production while maintaining consistent quality. Machines can operate continuously without breaks, fatigue, or error, leading to significant improvements in throughput. This level of efficiency is especially critical in high-demand industries where time-to-market is a key competitive factor. - Cost Reduction
While the initial investment in automation systems can be significant, the long-term cost savings are considerable. Automated systems reduce labor costs, minimize waste, and improve resource utilization. They also reduce the risk of costly errors or defects in the manufacturing process, leading to higher-quality products and fewer returns or warranty claims. - Improved Quality and Consistency
Automated systems provide a level of precision and repeatability that is difficult to achieve with manual labor. This leads to fewer defects, greater product uniformity, and higher overall quality. Automation also allows for continuous monitoring and adjustments in real-time, ensuring that the production process stays within tight tolerances. - Enhanced Safety
Automation can take over dangerous or physically demanding tasks, reducing the risk of injury to human workers. In industries such as chemical manufacturing or heavy machinery, robots can handle hazardous materials or perform tasks in extreme environments, keeping humans out of harm’s way. - Scalability and Flexibility
With automation, manufacturers can easily scale up or down depending on demand. Automated systems can be adjusted to accommodate larger volumes without significant changes in infrastructure. Flexible automation, in particular, allows for quick adaptation to new products or changing market conditions, making it easier to meet customer demands.
Challenges in Implementing Automation
Despite its numerous benefits, manufacturing automation presents several challenges. One of the most significant barriers is the high upfront cost of implementing automated systems. Small and medium-sized manufacturers may find it difficult to justify the investment, especially when profit margins are tight. Additionally, the transition to automation often requires a shift in workforce skills, necessitating training or hiring workers with expertise in managing and maintaining automated systems.
Another challenge is the integration of automation into existing processes. For many manufacturers, automation requires rethinking and redesigning workflows, supply chains, and even product designs to accommodate new technologies. This process can be time-consuming and disruptive if not properly planned.
There is also the issue of cybersecurity. As manufacturing systems become more connected and reliant on data, they become vulnerable to cyberattacks. Protecting automated systems from breaches or data theft is critical to ensuring the continued safety and reliability of operations.
The Future of Manufacturing Automation
The future of manufacturing automation lies in the convergence of AI, IoT, and advanced robotics. Factories of the future will be fully connected, with smart machines that communicate and collaborate with each other to optimize production processes in real-time. Predictive analytics will allow manufacturers to anticipate equipment failures before they happen, reducing downtime and maintenance costs.
Furthermore, advancements in additive manufacturing (3D printing) are likely to transform automation in industries where customization and rapid prototyping are key. Manufacturers will be able to produce parts and products on demand, reducing inventory costs and lead times.
In conclusion, manufacturing automation is no longer a distant future but a present reality that is reshaping industries across the globe. By embracing these technologies, manufacturers can not only stay competitive but also drive innovation and sustainable growth.
Please click here to follow us.