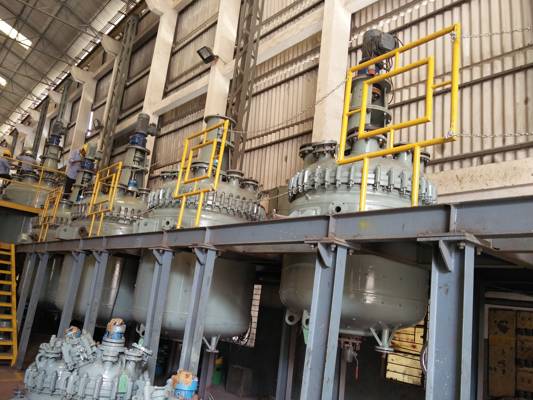
Industries such as chemicals, pharmaceuticals, and food processing deal with a wide range of chemicals, temperatures, and pressures in their daily operations. Having a glass lined reactor that is designed specifically for these conditions can improve efficiency, safety, and productivity. Off-the-shelf reactors may not always provide the best solution, especially if your operations involve unique challenges.
Customization allows a glass lined reactor manufacturer to modify the equipment to meet the exact requirements of your process. Whether you need additional safety features, specific sizes, or unique designs, these customizations ensure that your reactor functions optimally within your setup.
Key Customization Options Available
- Size and Capacity Adjustments The most basic form of customization involves adjusting the size and capacity of the reactor. Depending on the scale of your operations, you may need a larger or smaller reactor. A glass lined reactor manufacturer can design reactors in various sizes to suit your needs, ensuring that your reactor is neither too large nor too small for your production requirements.
- Temperature and Pressure Modifications Different processes require different temperature and pressure ranges. For example, pharmaceutical manufacturing may need precise temperature control, while chemical processes might involve handling high pressures. Manufacturers offer customization to accommodate these conditions, designing reactors that can safely operate under specific temperature and pressure settings.
- Unique Mixing and Agitation Systems Many processes require the mixing of chemicals inside the reactor. A glass lined reactor manufacturer can customize the mixing and agitation systems to match the needs of your process. Whether it’s a gentle stir for sensitive ingredients or more vigorous mixing for tougher materials, manufacturers can design the right agitation system to ensure effective and safe mixing.
- Special Coatings and Linings Glass lined reactors are known for their chemical resistance, but not all chemicals are the same. Some may require extra protection due to their corrosive nature. Manufacturers can apply special coatings or extra layers of glass to enhance the reactor’s durability and resistance to specific chemicals. This extra protection ensures that the reactor remains in good condition over time, even when handling aggressive substances.
- Outlet and Inlet Configurations The placement and design of the reactor’s inlet and outlet ports can be customized as well. Different processes may require specific configurations to ensure smooth flow in and out of the reactor. A glass lined reactor manufacturer can modify the number, size, and positioning of these ports to match the needs of your setup, making it easier to integrate the reactor into your production line.
- Advanced Safety Features Safety is a top priority in industries dealing with hazardous materials. Custom reactors can come with enhanced safety features such as pressure relief valves, temperature sensors, and emergency shutdown systems. These features help monitor and control the reactor, ensuring that your processes remain safe and efficient at all times.
- Automation and Control Systems Modern industrial processes often involve automation, and a glass lined reactor manufacturer can equip your reactor with automated control systems. These systems allow for easier monitoring and control of the reactor’s temperature, pressure, and mixing. With automation, you can reduce the need for manual intervention, lower the risk of human error, and increase overall efficiency.
- Jacket and Heating Options Many processes require the reactor to be heated or cooled. Manufacturers offer customization options for jacketed reactors, which allow for the circulation of heating or cooling fluids around the reactor body. You can choose between steam, water, or oil jackets, depending on the heating or cooling needs of your process. This customization helps maintain the required temperatures inside the reactor for optimal performance.
Benefits of Customizing Your Glass Lined Reactor
- Improved Efficiency A customized reactor is designed to work seamlessly with your specific process. This means that you can expect smoother operations, fewer interruptions, and less downtime. Whether it’s faster mixing or better temperature control, a customized reactor helps improve the overall efficiency of your production line.
- Better Safety Customizing your reactor with additional safety features can help protect your workers and equipment. With proper monitoring and control systems in place, you can reduce the risk of accidents, ensuring a safer work environment.
- Cost-Effective in the Long Run While custom reactors may have a higher initial cost, they often prove to be more cost-effective in the long run. A reactor tailored to your process will last longer, require less maintenance, and reduce the chances of breakdowns. This means fewer repairs and lower operational costs over time.
- Flexibility for Future Needs A glass lined reactor manufacturer can also design reactors that offer flexibility for future expansions or process changes. This means that if your production needs grow or change over time, your reactor can be modified or adapted without the need for a complete replacement.
- Enhanced Product Quality When your reactor is customized to suit your specific process, you can expect better consistency and higher product quality. Whether it’s ensuring proper mixing or maintaining precise temperatures, a custom reactor helps produce better end products, which is crucial in industries like pharmaceuticals and food processing.
Conclusion
Customization is key when it comes to ensuring that your glass lined reactor meets the unique requirements of your industrial process. A glass lined reactor manufacturer offers a wide range of customization options, from size and capacity adjustments to advanced safety features and automation. By investing in a custom reactor, you not only ensure that your equipment is optimized for your specific needs but also improve the efficiency, safety, and quality of your production process.
Excellent posts Thanks a lot.
casino en ligne fiable
Kudos! A good amount of information.
casino en ligne
Amazing lots of superb knowledge!
casino en ligne France
Cheers, A lot of facts!
casino en ligne
Many thanks! Excellent information!
casino en ligne francais
Incredible all kinds of amazing information.
casino en ligne France
You said it fantastically.
casino en ligne France
Nicely put, Thanks.
casino en ligne
Perfectly voiced of course. !
casino en ligne France
Wow plenty of superb material.
casino en ligne