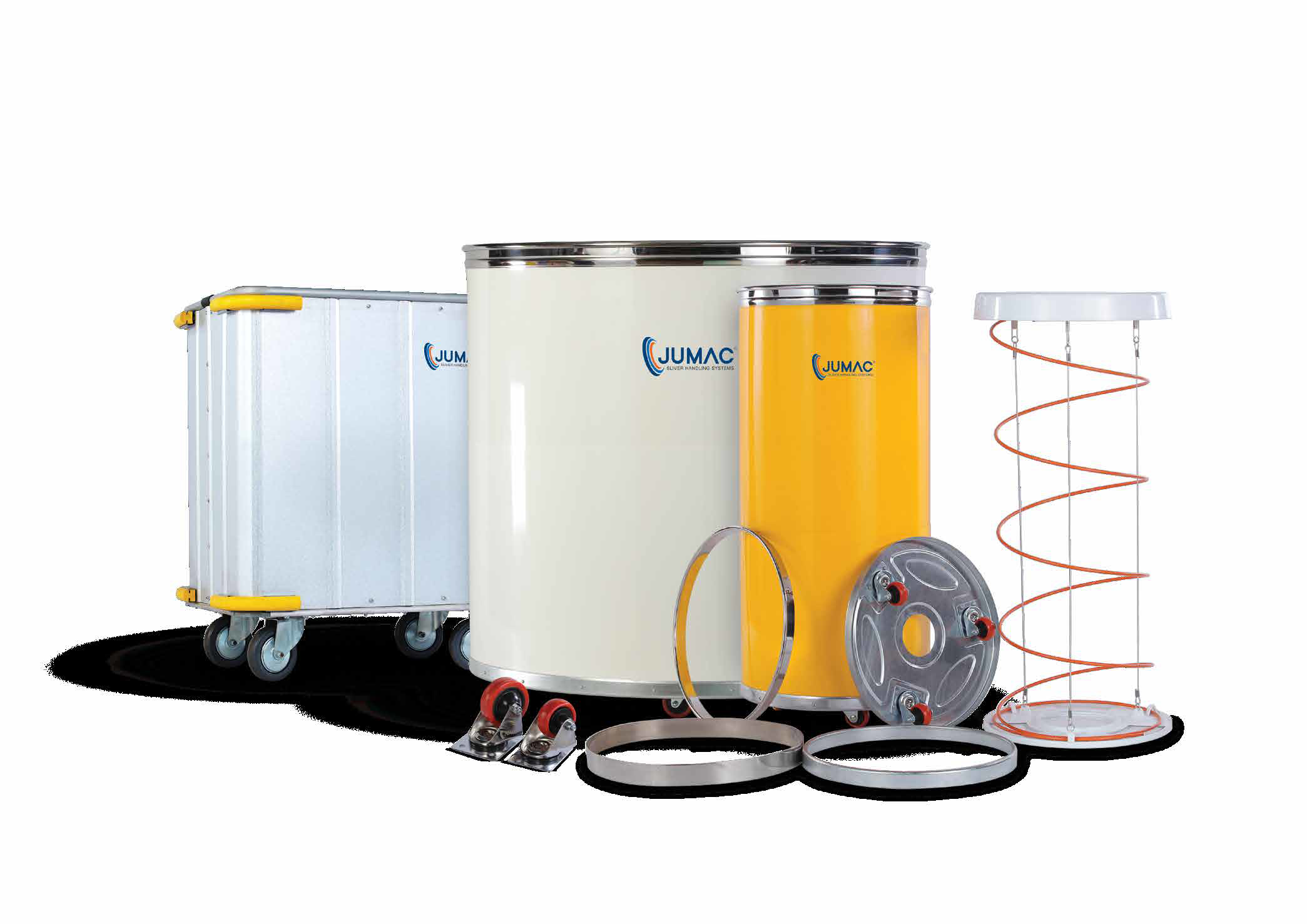
Spinning can accessories play a very significant role in enhancing the productivity of spinning mills. This includes essential accessories for the spinning industry, such as precision springs, HDPE (High-Density Polyethylene) sheets, and premium caster wheels. Well-designed accessories prevent loosening or fibre loss, enhancing the overall productivity of the spinning process. Here’s how they enhance the overall operational efficiency in the textile factories by contributing to improving overall machine outputs.
Enhanced operational performance
Generally, the operational performance in the spinning industry greatly depends on the quality of the can accessories used. Optimising these ensures that these accessories support maximum efficiency while maintaining control over material handling. For instance, top and bottom ring plates and covers are among the equipment that ensure continuous operation while guarding the sliver. Additionally, anti-static agents in the body sheets (HDPE) neutralise static charges, preventing dust adhesion on the can and maintaining sliver quality.
Better sliver handling
Spinning can accessories are essential for enhancing handling by ensuring smooth and consistent sliver movement throughout the spinning process. One of the major issues in sliver handling is breakage which essentially leads to a cutdown in production rate. Precision springs and other accessories reduce the stress on the sliver with better load management even under varying loads. On the other hand, premium caster wheels facilitate the smooth transfer of slivers from cans to spinning frames, promoting continuity in material flow. This also enables better control over the sliver and reduces fibre breakage.
Enhanced load management
Spinning can accessories improve load management by preventing overloading and maximising capacity, leading to enhanced machine performance and a more efficient production procedure. Precision springs, for example, are carefully calibrated to support the required skiver weight and precisely tempered with heat treatment for proper alignment of the sliver. Box-type springs in spring cans maintain the sliver’s constant height during rotor spinning, enhancing load-bearing capability and stability throughout operations. Pantograph springs possess a crisscross design and ensure that the unique properties of the sliver remain intact. They are heat-treated for harder and fatigue-resistant properties. These springs reduce yarn defects due to the smooth movement of the sliver. It maintains sliver equilibrium even when changes in loading take place.
Ensuring uniform material movement
Spinning can accessories play a crucial role in ensuring uniform material movement with minimal breakages in production processes. Uniform movement of material flow here simply refers to the free flow of sliver from one stage of the manufacturing process to the next. The spinning cans are designed to carry slivers while maintaining consistent feeding, minimising the need for frequent replacements. This enables a steady and consistent flow of materials through the production line, improving the overall operational efficiency.
Minimisation in waste material
The accessories of spinning cans play a crucial role in enhancing operational efficiency. Key components include HDPE sheets, caster wheels, top and bottom covers, and springs. Each element contributes to effective sliver handling, ensuring a smooth production process. The HDPE sheets provide durability, while the caster wheels enable easy manoeuvrability, allowing for seamless movement of cans throughout the facility.
Moreover, the top and bottom covers protect the sliver from external elements, preventing contamination and damage. Springs are essential for maintaining the proper tension, ensuring that sliver remains intact during transport. Together, these accessories minimise waste and enhance the overall productivity of spinning operations, ultimately leading to better quality and reduced costs.
Conclusion
It’s clear that spinning accessories play a crucial role in enhancing production processes within the textile industry. By optimising these tools, the production quality and efficiency in the overall operational process can be significantly enhanced. Improved handling of slivers by design and attachment can incorporate better quality, less waste, and less downtime. A well-designed material handling system can significantly increase production efficiency by reducing dependency on labour and ensuring a smoother flow of goods throughout the entire process. Moreover, embracing the principles of lean manufacturing, recycling and reusing resources can go a long way in reducing waste and increasing productivity and profitability.
With a reputation built on trust from 2000+ spinning mills and leading textile companies across 6 continents, Jumac is esteemed as the preferred partner for sliver handling solutions. Jumac’s commitment to innovation and customer satisfaction has positioned it as a leader in the industry, continually adapting to market needs and offering tailored solutions to meet diverse operational requirements. For over 50 years, it has consistently expanded its international client base by investing in state-of-the-art infrastructure, delivering superior machine quality, and providing excellent customer service.