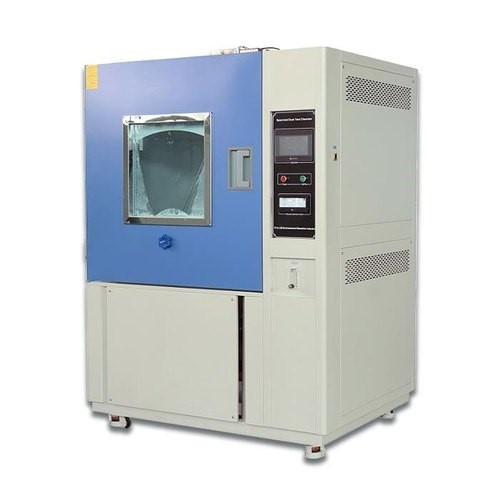
In an era of paramount quality, industries increasingly turn to innovative solutions to ensure their products meet the highest standards. One such solution is the use of testing chambers. These versatile tools are designed to simulate various environmental conditions, allowing companies to assess their products’ durability, reliability, and overall performance. This article will explore how testing chambers contribute to quality assurance across different industries and the key benefits they provide.
What Are Testing Chambers?
Testing chambers, or environmental test chambers, are controlled environments replicating specific conditions such as temperature, humidity, and pressure. These chambers enable manufacturers to conduct rigorous tests on their products to identify potential weaknesses before they reach the market.
Why Are Testing Chambers Important?
- Product Reliability: Testing chambers help ensure products perform as expected under different environmental conditions.
- Regulatory Compliance: Many industries have strict regulations that require testing to verify product quality and safety.
- Cost Efficiency: By identifying design flaws early in development, companies can save money on recalls and repairs.
How Testing Chambers Work
Testing chambers are equipped with advanced technology for precise control of environmental variables. Here’s how they function:
- Temperature Control: Chambers can simulate various temperatures, from extreme cold to extreme heat.
- Humidity Control: They can maintain specific humidity levels, allowing for the testing of how moisture affects materials.
- Pressure Control: Some chambers can simulate high-altitude conditions, evaluating how products perform under reduced pressure.
Manufacturers can conduct various tests by creating these controlled environments, including thermal cycling, humidity exposure, and mechanical stress tests.
Industries That Benefit from Testing Chambers
1. Electronics and Electrical Industry
In the electronics industry, reliability is crucial. Components are often exposed to extreme conditions, and any failure can lead to significant safety issues.
Testing Applications:
- Thermal cycling tests ensure components can withstand temperature fluctuations.
- Humidity tests evaluate how moisture affects circuit boards and electronic devices.
Example: A smartphone manufacturer might use a thermal shock chamber to ensure their devices can handle rapid temperature changes when transitioning from indoor to outdoor environments.
2. Aerospace and Aviation
The aerospace industry operates under some of the most rigorous standards, where failure is not an option.
Testing Applications:
- Altitude chambers simulate high-altitude conditions to test components like avionics.
- Environmental chambers evaluate how materials withstand harsh conditions during flight.
Example: An aerospace company may use an altitude chamber to test the durability of engine components at high elevations, ensuring they perform reliably under reduced atmospheric pressure.
3. Pharmaceuticals and Healthcare
Quality assurance in the pharmaceutical industry is critical, as even minor defects can have profound health implications.
Testing Applications:
- Humidity chambers test the stability of medications and vaccines under various moisture levels.
- Temperature chambers ensure that storage conditions meet regulatory requirements.
Example: A pharmaceutical company might use a humidity chamber to assess how a new vaccine performs over time in different humidity levels, ensuring efficacy before it reaches the market.
4. Automotive Industry
The automotive industry requires rigorous testing to ensure that vehicles can withstand various environmental conditions.
Testing Applications:
- Temperature and humidity tests ensure vehicle materials don’t degrade over time.
- Corrosion tests assess how components react to salt and moisture.
Example: An automotive manufacturer might use environmental chambers to test the durability of paints and coatings on vehicles exposed to extreme weather conditions.
5. Food and Beverage Industry
Quality assurance in the food and beverage industry is essential to prevent spoilage and ensure safety.
Testing Applications:
- Humidity and temperature testing evaluate how packaging materials perform under different storage conditions.
- Shelf-life studies help determine how long products can last before degrading.
Example: A food manufacturer might use a humidity chamber to test how packaging material keeps food fresh under various moisture conditions, ensuring product quality upon delivery.
Critical Benefits of Testing Chambers
1. Enhanced Product Quality
Testing chambers allow companies to identify and rectify issues before products reach consumers. By simulating real-world conditions, manufacturers can enhance product quality and reliability.
2. Reduced Costs
Early identification of defects can lead to significant cost savings. Companies can avoid costly recalls and repairs by ensuring products meet quality standards before market.
3. Compliance with Regulations
Many industries face stringent regulations requiring testing for safety and performance. Testing chambers help companies meet these requirements, avoiding legal complications and ensuring consumer safety.
4. Increased Customer Satisfaction
Quality products lead to satisfied customers. Companies can enhance customer trust and loyalty by using testing chambers to ensure products perform reliably.
5. Innovation and Development
Testing chambers enable companies to experiment with new materials and designs. This fosters innovation and encourages the development of cutting-edge products that can stand out in a competitive market.
Frequently Asked Questions
1. What types of tests can be conducted in testing chambers?
Testing chambers can perform a variety of tests, including:
Thermal cycling
Humidity exposure
Corrosion testing
Mechanical stress tests
2. How do I choose the right testing chamber for my needs?
Consider the following factors:
Environmental conditions to be simulated
Size and capacity requirements
Budget constraints
Specific industry regulations
3. Are testing chambers customizable?
Many manufacturers offer customizable options to tailor chambers to specific testing requirements. Discuss your needs with suppliers for the best solutions.
4. How often should testing chambers be calibrated?
Regular calibration is essential for accurate results. Generally, it is recommended to calibrate testing chambers at least once a year or after significant usage.
5. What maintenance is required for testing chambers?
Regular maintenance includes:
Routine cleaning of the chamber interior
Calibration checks
Inspection of seals and insulation
Conclusion
Testing chambers play a vital role in ensuring quality across various industries. These versatile tools, from electronics to pharmaceuticals, help manufacturers identify potential issues, comply with regulations, and enhance product reliability. Investing in the proper testing chamber can lead to significant cost savings, improved customer satisfaction, and a more robust market presence.
For more information on testing chambers and to explore various options available, visit [Technical Products](https://technicalproducts.in/testing-chambers/). By leveraging the power of testing chambers, companies can ensure their products meet and exceed industry standards, fostering a culture of quality and innovation.