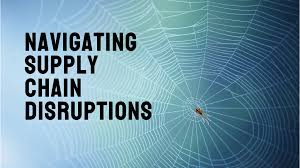
Introduction
The construction industry operates within a complex ecosystem where the success of each project relies heavily on the smooth flow of materials, equipment, and skilled labor. However, in recent years, this industry has faced a significant hurdle: supply chain disruptions. These disruptions, triggered by various factors such as natural disasters, global pandemics, trade disputes, and transportation challenges, have caused delays, escalated costs, and created logistical headaches for construction project management worldwide.
Understanding the Root Causes
One of the leading causes of supply chain disruptions in construction is the global interconnectedness of the industry. When materials are sourced from across the globe, even a minor hiccup can create a ripple effect that disrupts timelines on a construction site thousands of miles away. For instance, a factory shutdown in one country can lead to a critical shortage of construction components, impacting multiple projects simultaneously.
The Impact on Construction Projects
Delays, Rising Costs, and Penalties:
Supply chain disruptions can quickly derail construction schedules, leading to a cascade of delays. Missed deadlines result in additional costs, including extended labor, overheads, and potential penalties for late project delivery. Moreover, expedited shipping, sourcing alternative materials at higher prices, or paying overtime to mitigate delays can significantly inflate the project budget.
Effects on Project Quality and Timelines:
Material shortages may necessitate substitutions, which can compromise the intended design and quality standards. Time-sensitive phases of construction are particularly vulnerable, with delays in one stage often causing a domino effect that elongates the overall project timeline.
Strategies for Managing Disruptions
While supply chain disruptions can feel overwhelming, construction companies can adopt proactive measures to navigate these challenges more effectively:
Diversifying Suppliers: Relying on a single supplier for critical materials is a risky strategy. By diversifying your sources, you can mitigate risks associated with disruptions from specific regions or suppliers.
Enhancing Communication and Collaboration: Open lines of communication with suppliers, contractors, and stakeholders are essential. Staying informed about potential issues allows for better planning and quicker adaptation to changing circumstances.
Integrating Technology: Embrace technology to gain real-time visibility into your supply chain. Utilizing software to track shipments and monitor inventory levels can provide the insights needed to anticipate and address disruptions before they escalate.
Contingency Planning: Having contingency plans in place is invaluable. Identifying backup suppliers or alternative materials in advance can help minimize delays when disruptions occur.
Embracing Adaptability and Flexibility: Flexibility is key to managing supply chain disruptions. Be prepared to adjust project timelines, redesign aspects of the project, or modify construction schedules based on the availability of materials.
Conducting Risk Assessments and Mitigation: Regularly assess potential risks within your supply chain and develop strategies to mitigate these risks. A proactive approach to risk management can help you stay prepared for unforeseen events.
Conclusion
Understanding the root causes and impacts of supply chain disruptions is crucial for devising effective strategies to manage them. By implementing contingency plans, diversifying suppliers, leveraging technology, and fostering a culture of collaboration and adaptability, construction companies can mitigate the effects of supply chain disruptions and ensure project success despite these challenges. With a forward-thinking approach, the industry can continue to thrive even in the face of supply chain uncertainties.