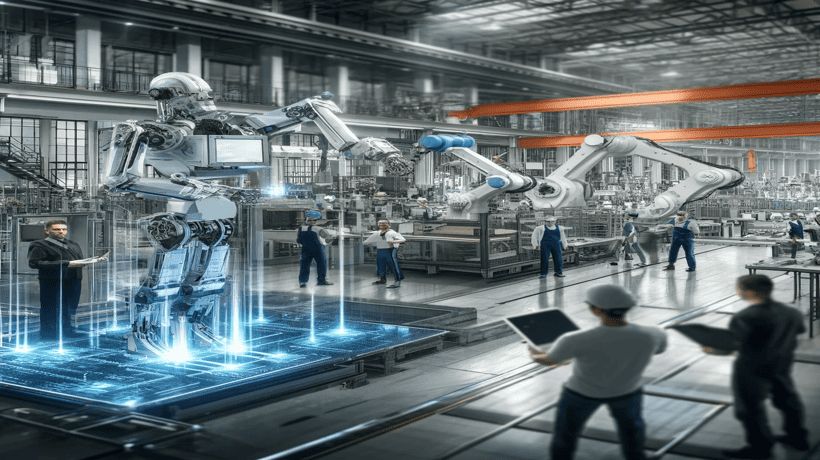
Key Highlights
Industrial automation integrates advanced technologies into manufacturing processes to enhance efficiency and productivity. The spectrum of industrial automation systems includes fixed, programmable, flexible, and integrated systems. The benefits of adopting industrial automation are manifold, including increased production output, improved product quality, cost savings, enhanced workplace safety, and mitigation of labor shortages. Successfully implementing industrial automation requires meticulous planning and the creation of custom solutions tailored to specific operational needs, while also addressing common challenges. The future of industrial automation is promising, with the integration of AI and robotics, offering new avenues for business growth and competitive advantage. Mastering these automation technologies can significantly elevate a company’s standing in today’s dynamic manufacturing landscape.
What is Industrial Automation?
Industrial automation involves utilizing control systems such as computers, robots, and information technologies to handle different industrial processes and machinery, replacing or augmenting human intervention. The primary goals of industrial automation are to enhance operational efficiency, productivity, and safety in manufacturing processes.
Understanding the Basics of Industrial Automation
Industrial automation leverages various technologies and systems to streamline industrial tasks, reducing the need for manual intervention. It involves the integration of machines, sensors, and control systems to optimize production processes, making them faster and more reliable. Automation technology enables businesses to achieve higher throughput, enhance safety, lower operational costs, and minimize errors. This technology is applicable across diverse industries such as manufacturing, automotive, healthcare, and more. By revolutionizing industrial operations, automation helps businesses improve overall efficiency, making processes smoother and more consistent with minimal human input.
Defining Industrial Automation and Its Importance
Industrial automation entails the use of sophisticated machinery and technology to simplify industrial tasks, speeding up processes while reducing the necessity for human labor. It integrates machines, sensors, and control systems to ensure seamless operation of production lines. This approach not only minimizes errors and costs but also enhances product quality by automating repetitive or labor-intensive tasks.
For businesses aiming to enhance operational efficiency and maintain a competitive edge, industrial automation is crucial. By automating tasks, companies can increase production speed, improve product quality, and reduce dependency on manual labor, thus lowering the risk of errors and inconsistencies. Automation also allows workers to focus on more value-added tasks, leading to overall productivity gains.
Exploring the Different Types of Industrial Automation Systems
Various types of industrial automation systems cater to different operational needs. Understanding these types can help companies choose the most suitable system for their production requirements:
- Fixed Automation: Designed for repetitive tasks, fixed automation is ideal for mass production of identical items. It involves dedicated equipment for specific processes, ensuring high production rates.
- Programmable Automation: This type allows for flexibility in manufacturing different products. It uses computer-controlled machinery that can be reprogrammed for different tasks, making it suitable for batch production.
- Flexible Automation: Combining the features of fixed and programmable automation, flexible automation uses robots and smart systems capable of handling multiple tasks. It is adaptable and can be quickly reconfigured to accommodate changes in production needs.
- Integrated Automation: This system integrates fixed, programmable, and flexible automation into a unified operation. It offers comprehensive control over production processes, enhancing efficiency and productivity.
By exploring these options, companies can determine the best system to align with their production goals, reducing human intervention and optimizing efficiency.
The Key Components of Industrial Automation
Industrial automation systems comprise several critical components that work together to automate factory tasks and processes. These components include sensors, actuators, control systems, and interfaces. Each plays a vital role in ensuring seamless communication, data collection, and decision-making within the automation system.
Sensors and Actuators: The Building Blocks
In automation systems, sensors and actuators are essential. Sensors act as the eyes and ears of machines, monitoring variables such as temperature, pressure, and humidity. Actuators, on the other hand, execute actions by converting electrical signals into physical movements.
Together, sensors and actuators reduce manual labor by automating tasks, ensuring smooth and fast operations. Sensors provide real-time data that actuators use to perform precise actions, enhancing operational efficiency and reducing errors.
Control Systems and Interfaces for Effective Operation
Control systems and interfaces are crucial for the effective functioning of industrial automation. Programmable Logic Controllers (PLCs) manage operations, ensuring that different parts of the system work together seamlessly.
Supervisory Control and Data Acquisition (SCADA) systems gather real-time data from sensors, providing operators with visual representations of the production process. Human-Machine Interfaces (HMIs) enable operators to monitor and control operations, ensuring smooth and efficient functioning of the automation system.
Strategies for Implementing Industrial Automation
Implementing industrial automation requires careful planning and strategic decision-making. Here are some steps to ensure a successful transition:
- Identify Objectives: Define clear goals for automation, such as improving product quality or increasing production speed. Identify which tasks or processes will benefit most from automation.
- Evaluate Options: Research available automation tools and technologies to find those that best fit your existing systems and future needs.
- Conduct a Cost-Benefit Analysis: Assess the financial viability of automation by comparing upfront costs with potential long-term savings and productivity gains.
- Develop an Implementation Plan: Create a detailed roadmap outlining the steps for integrating automation, including system integration, employee training, and maintenance.
- Seek Professional Advice: everages various technologies and systems to streamline industrial tasks, reducing the need for manual intervention. It encompasses several types of automation systems:
Types of Industrial Automation Systems
- Fixed Automation: Also known as hard automation, this system is characterized by high production rates and is used for repetitive tasks. The equipment is specifically designed for a particular function, offering little flexibility but high efficiency for mass production.
- Programmable Automation: This type allows for reprogramming of machines to accommodate different tasks or products. It offers flexibility and is commonly used in batch production processes.
- Flexible Automation: Also known as soft automation, it enables the production of different products with minimal changeover time. This system is highly adaptable and ideal for producing small to medium-sized batches.
- Integrated Automation: This encompasses the complete automation of manufacturing processes through the integration of various subsystems. It often involves the use of advanced software and communication technologies to create a cohesive and efficient production environment.
Benefits of Industrial Automation
Implementing industrial automation in manufacturing processes offers numerous benefits:
Increased Production Output
Automation systems can operate continuously without fatigue, significantly boosting production rates. They can also work at higher speeds than human workers, leading to greater output.
Improved Product Quality
Automated systems maintain consistent performance, reducing the risk of errors and defects. This results in higher quality products and increased customer satisfaction.
Cost Savings
Automation reduces labor costs by minimizing the need for manual labor. It also lowers operational costs through improved efficiency and reduced waste.
Enhanced Workplace Safety
By automating hazardous tasks, companies can protect workers from dangerous environments, reducing the risk of accidents and injuries.
Mitigation of Labor Shortages
Automation helps address labor shortages by filling gaps in the workforce, especially for repetitive or physically demanding tasks.
Challenges in Implementing Industrial Automation
Despite its numerous benefits, implementing industrial automation can be challenging. Common obstacles include:
High Initial Costs
The upfront investment in automation technology can be substantial. However, the long-term savings and efficiency gains often justify the initial expenditure.
Technical Complexity
Integrating automation systems requires specialized knowledge and expertise. Companies must invest in training their workforce to manage and maintain these systems.
Resistance to Change
Employees may resist the introduction of automation due to fear of job loss or changes in work processes. Effective change management and communication are essential to address these concerns.
Customization Needs
Each manufacturing process is unique, and automation solutions must be tailored to specific needs. This customization can be time-consuming and costly.
Steps for Successful Implementation
Successfully implementing industrial automation involves several key steps:
1. Assess Needs and Goals
Identify the specific needs and goals of your manufacturing process. Determine which tasks can benefit most from automation and set clear objectives for the implementation.
2. Conduct a Cost-Benefit Analysis
Evaluate the potential benefits and costs of automation. Consider factors such as increased production, cost savings, and improved quality against the initial investment and ongoing maintenance costs.
3. Develop a Detailed Plan
Create a comprehensive implementation plan that outlines the steps, timelines, and resources required. Include provisions for training, integration, and testing.
4. Choose the Right Technology
Select the appropriate automation technology based on your needs and goals. Consider factors such as scalability, flexibility, and compatibility with existing systems.
5. Train Your Workforce
Invest in training programs to equip your workforce with the necessary skills to manage and maintain the automation systems. Effective training is crucial for successful implementation and ongoing operation.
6. Monitor and Optimize
Continuously monitor the performance of your automation systems and make necessary adjustments to optimize efficiency and productivity. Regular maintenance and updates are essential to ensure long-term success.
The Future of Industrial Automation
The future of industrial automation is bright, with emerging technologies such as artificial intelligence (AI) and robotics poised to revolutionize manufacturing processes. AI-driven automation can enhance decision-making, predictive maintenance, and quality control. Robotics can further automate complex tasks, increasing efficiency and flexibility.
Embracing AI and Robotics
By integrating AI and robotics into automation systems, companies can achieve higher levels of efficiency and productivity. These technologies enable more intelligent and adaptive manufacturing processes, providing a competitive edge in the market.
Sustainability and Industrial Automation
Automation can also contribute to sustainability by reducing waste, energy consumption, and emissions. Smart manufacturing processes can optimize resource use, leading to more sustainable production practices.
Preparing for the Future
To stay competitive, companies must embrace the advancements in industrial automation. Continuous learning and adaptation are crucial for leveraging these technologies to their fullest potential.
Conclusion
Industrial automation is transforming manufacturing processes, offering significant benefits in terms of efficiency, productivity, and quality. While the implementation of automation systems can be challenging, the long-term advantages outweigh the initial hurdles. By understanding the basics, benefits, and challenges of industrial automation, and following a structured implementation plan, companies can unlock new levels of performance and competitiveness. Embracing future technologies such as AI and robotics will further enhance the capabilities of industrial automation, paving the way for a more efficient and sustainable manufacturing landscape.